Slot Die Coating Design
Written by Mary O'Kane, who is pursuing a PhD in Perovskite Solar Cells at the University of Sheffield in collaboration with Ossila Ltd. As part of this, she shares her knowledge with Ossila customers by creating helpful guides on solution-processing methods. |
Slot die coating enables even distribution of a pre-metered coating to be applied to a substrate. In many cases a slot die can increase production speeds and improve coat weight control. The slot die is used in conjunction with a rubber or precision steel backing roll to apply coating to the substrate. Slot die coating hot melt adhesives requires specialist systems to suit the specific requirements. Universal Converting Equipment is able to offer a range of slot die coating systems developed by Universal Adhesive Systems, ITW Dynatec and other manufacturers of slot dies. We undertake the design and manufacturing of complete slot die coating turnkey systems including: fixed slot dies, fluid delivery systems, vacuum systems, filtration systems, die coating stations, and other ancillary equipment. Range of Capabilities. Die Flatness: Our standard is 2.54 µm (0.0001”); however, we have the capability of.

When it comes to depositing highly-uniform wet thin films, there are many different solution-processing techniques capable of producing high-quality films at low cost. Each processing technique has its own unique advantages and disadvantages, as well as critical parameters that must be monitored carefully to achieve desired coatings. These parameters determine the quality of the resulting thin films.
This guide compares several popular solution-processing techniques, and explores their strengths and weaknesses. By understanding the differences between these techniques, you will know how to choose the appropriate coating method for your experimental needs.
Contents
Dip Coating
During dip coating, the substrate is immersed in the coating solution. As it is withdrawn, a liquid layer is entrained on the substrate. The thickness of this entrained solution is determined by the withdrawal speed.
For more information on how film thickness is controlled, you can visit our guide Dip Coating Theory: Film Thickness; for information on common coating defects, you can visit Dip Coating: Guide to Troubleshooting Defects.
Advantages
- Simple process and setup. You do not need extensive training to start, and specific thicknesses can be obtained by controlling a few parameters.
- Good for coating on flat substrates. Can also be adapted to coat other surfaces (such as tubes). Coats both sides of a flat substrate at once.
- Very uniform coatings can be created, with surface roughness of nanometres.
- Gradient coatings can be achieved by varying the withdrawal speed.
- Adaptable between high-precision batch processes and large-scale processes.
- By lowering withdrawal speeds, the process can be optimised for use with low-concentration solutions.
- Less expensive set-up than other techniques (e.g. slot-die coating).
- Small size of equipment - the total bench area of the Ossila Dip Coater is 10 cm x 30 cm - you can use this technique in small labs.
- Significant drying time. Good for when time is needed to allow film structure formation.
Disadvantages
- During the drying phase, the wet film is vulnerable to environmental factors (e.g. turbulent air flow). Such factors need to be actively controlled, so the drying phase would ideally be done in a cleanroom.

- Difficult to coat curved or flexible substrates.
- Depending on the solution, the film can require post-deposition heat treatment. This can mean that fewer substrates can be deposited onto, thus increasing the cost of process. This also makes scaling more difficult.
- Material shrinkage (when changing from a liquid to a solid layer) can lead to cracking in films. This effect is worsened for thicker films.
- Dip coating requires a reservoir of solution for the substrate to be immersed in. To achieve a uniform coating, it is important that the volume of the solution is far greater than the volume of the substrate. This can lead to a high quantity of solution wastage.
Ideal Use
Dip coating was developed for use in large-scale manufacturing, and is suitable for incorporation into roll-to-roll processing. However, it can also be used in small-batch experiments. As dip coating is affordable, easy to master, and easily adaptable to suit different needs, the process is often used in research for simple thin-film coatings. Dip coating is ideal for coating both sides of a flat substrate simultaneously, and can be used to create gradient coatings by varying withdrawal speed. The technique is often used in research on protein coatings, protective coatings, and tribiological coatings.
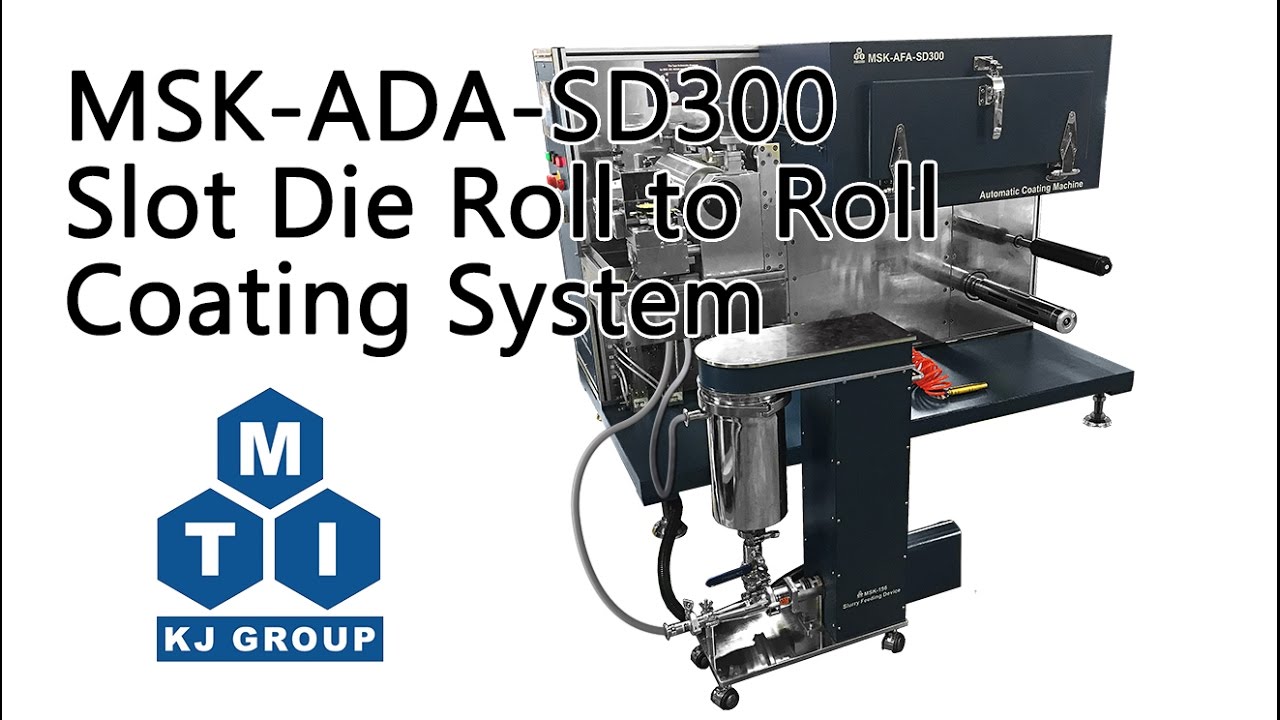
Spin Coating
In spin coating, the solution is dispensed onto a flat substrate which is either already rotating, or subsequently begins to rotate. The centripetal force shears the solution, causing it to be distributed evenly across the surface as a thin film. The thickness of the deposited film is determined by the shearing force applied, which is proportional to the rate of rotation.
A detailed explanation of the theory and processes that determine film thickness can be found at Spin Coating: Guide to Film Thickness. A helpful guide on how to overcome problems with troublesome solutions can be found at Spin Coating: Guide to Coating Difficult Solutions. Lastly, an in-depth discussion of the technique can be found at Spin Coating: A Guide to Theory and Techniques.
Advantages
- This is a simple and effective process which can be mastered with little training.
- Coats small, flat substrates extremely well.
- Can achieve thin uniform films with a wide range of thicknesses (from nm to microns).
- Fast drying time (due to the substrate rotating) means that films can be created very quickly.
- Post-deposition heat treatment is not always necessary, as the airflow created by the rotation can be enough to dry the film.
- Uniform drying is assisted by the airflow generated during the film's rotation.
- The most cost-effective of all these methods for creating individual films, as it does not require any high energy processes.
Disadvantages
- The main limitations of spin coating are that it is only effective for coating small substrates, and is limited to batch processing. Spin coating is completely unsuitable for large-scale production, so this limits its applications to research and development.
- During spin-coating, a lot of the ink is cast off. This process has high levels of solution wastage. Additionally, this can make it difficult to coat with a low-concentration solution.
- Cannot create films on curved surfaces, and is difficult to use when coating flexible surfaces.
- Cannot create gradient thickness across the films – creates a film of uniform thickness.
- Drying times involved in spin coating are often short, so it is not suitable for processes that require extended drying times.
Ideal Uses
Spin coating quickly and reliably produces uniform films over a small surface area. It is perfect for use in research and development laboratories working on a wide range of thin-film technologies. Additionally, spin coating is cost-effective and easy to set up and use, making it popular across a wide range of research fields. Spin coating is often used in processing photoresists on wafers and for thin film electronic devices (such as photovoltaics and light-emitting diodes).
Slot-Die Coating
Slot-die coating is a technique where solution is directly coated onto the substrate through a coating “head”. Solution flows through the head at a determined rate and the substrate is moved underneath it.
Slot-die coating is a metered coating process. This means that the wet film thickness is determined by the amount of solution placed onto the substrate. All other parameters work to improve the uniformity and stability of the coating. An in-depth discussion of the slot-die technique can be found in Slot-Die Coating: Theory, Design and Applications.
Advantages
- One major advantage of slot-die coating is that it is scalable. This means the process would work on an industrial scale. Additionally, it can be used in roll-to-roll processing. These factors make it ideal for use in manufacturing.
- Excellent uniformity films can be produced.
- Method is adaptable. It can work with high or low viscosity solutions and can be used to deposit a wide range of thicknesses.
- This is a pre-metered technique, so the flow of solution is very well controlled. There is very little solution waste.
- Can coat onto flexible substrates.
- High coating speeds can be achieved.
Disadvantages
- Slot-die coating is a significantly more complex process, with multiple parameters needing be optimised. To create high-quality thin films, a deep understanding of the physics behind each variable is needed. This technique requires more initial training than the other techniques.
- Very high initial setup cost compared to other techniques. It is a good investment if producing high-volume low-cost films, but is often too expensive for initial research and development. An affordable, reliable option is the Ossila Slot-Die Coater.
- As most commercial slot-die coaters cater more for manufacturing needs, large supporting infrastructure is often needed to house the equipment.
- Due to the complexity of the system there are more sources of defects making diagnosing issues difficult.
Ideal Uses
Slot-die coating is an excellent process to use when scaling up from development to manufacture. This is due to its low solution wastage, wide range of coating viscosities, and the high throughput speeds that can be achieved. It is good for coating one side of rigid or flexible substrates, and is used in thin-film electronics research - especially in photovoltaics and LEDs.
Doctor Blading
Doctor blading - also known as knife coating or blade coating - is a popular thin-film fabrication technique. It involves either running a blade over the substrate or moving a substrate underneath the blade. There is a small gap that determines how much solution can get through. Here, solution is effectively spread over the substrate.
The final thickness is a fraction of the gap between the substrate and the blade. The final thickness of the wet film will be influenced by the viscoelastic properties of the solution and the speed of coating..
Advantages
- This process is scalable, so this process could be used to create thin films on an industrial scale. This is extremely important when developing any device or product that will eventually go to market.
- Can create uniform thin films over large surface areas. Many techniques lose uniformity with scaling, but this method retains control.
- Fast process, creating thin films quickly and efficiently.

- Solution is deposited from a reservoir in a controlled manner. Therefore, there is less solution wastage during deposition (compared to dip coating and spin coating).
- This is a simple but versatile technique. Different factors (e.g. substrate speed or gap size) can be optimised to produce films of different thicknesses or at different speeds. It can also produce films from solutions with a wide range of viscosities.
- Inexpensive to set up and produces a high throughput.
- Can coat rigid or flexible substrates.
Disadvantages
- Cannot create films with thicknesses below 10s of microns.
- Not as precise as other techniques (e.g. spin coating). It is also very difficult to reach the same levels of uniformity.
- Any contamination with the system can lead to streaks being formed in the wet film as the blade is dragged close to the substrate.
- Patterning with this technique is not possible. Only uniform films across a substrate can be created.
- The wet layer film thickness has poor reproducibility. This is due to the shearing rate of the solution impacting the final film thickness.
Ideal Uses
Doctor blading is a technique that is well suited for large-scale coatings. The technique is also well suited for creating thicker films from a viscous solution. It cannot offer the nanoscale uniformity or extreme thin films that spin coating can. However, the scalability, versatility, and simplicity of this technique make it perfect for industrial use. It is also used across a wide range of research fields, including thin-film electronics, battery technology, ceramics, and paints.
Bar Coating
Bar coating - also known as Meyer bar coating - is very similar to doctor blading. An excess of solution is placed on the substrate and it is spread across by a bar. This bar is a spiral film applicator, and is essentially a long cylindrical bar with wire spiralling around it.
The gaps made between the wire and the substrate determine how much solution is allowed through. This subsequently determines film thickness.
Advantages
- This process is inexpensive and simple to use, while producing consistently uniform films.
- Multiwire & special wire designs allow you to change film properties (e.g. thickness) without changing the chemistry of the coating material or completely overhauling the system.
- Controllable drying time. Good for when time is needed to allow film structure formation.
- This process is easily scalable.
- Can create a uniform film on rigid or flexible substrates over large areas.
Disadvantages
- Thicknesses of films are limited to diameter of the wire, which leads to a minimum thickness of ~10 microns.
- Patterning with this technique is not possible. Only uniform films across a substrate can be created.
- Any contamination with the system can lead to streaks being formed in the wet film as the bar is dragged close to the substrate
- Gradients cannot be produced throughout the film. Thickness depends on bar structure and solution properties.
- Slow coating speeds. The maximum speed is determined by the rate at which the gaps can be filled via the capillary force.
Ideal Uses
The scalability and simplicity of this technique make it very appealing for both research and manufacturing sectors. Additionally, the technique is easily adaptable, making it ideal to experiment with. The technique shares many similarities with doctor blading whilst retaining additional simplicity - reproducibility is made easy thanks to fixed coating thickness bars. This technique is often used in the same fields as blade coating because of the similarities between the coating methods.
Summary
In the guide above, the advantages, disadvantages and ideal uses of various coating techniques have been discussed. The qualities of each technique have been summarised in the table below.
Dip Coating | Spin Coating | Slot-Die Coating | Doctor Blading | Bar Coating | |
---|---|---|---|---|---|
Cost | Low Systems range from £1,800 to £4,000 | Medium Systems range from £2,000 to £10,000 | High Smaller R+D models range £5,000 to £50,000 | Low Systems can range from £1,800 to £4,000 | Low Systems can range from £1,800 to £4,000 |
Scalability | Limited | Not Possible | Scalable | Scalable | Limited |
Complexity | Medium | Low | High | Medium | Low |
Uniform Thin-films Produced? | Yes | Yes | Yes | Yes - although not as uniform as other techniques | Yes - although not as uniform as other techniques |
Patterning In-Situ | Thickness only | No | Thickness & simple 2D patterns | Thickness only | No |
Coatable Surfaces | Complex, rigid shapes. Roll-to-roll processable | Small, flat substrates only | Flexible or rigid substrates. Roll-to-roll processable | Flexible or rigid substrates. Roll-to-roll processable | Flexible or rigid substrates. Roll-to-roll processable |
Solution Wastage | High | High | Low | Moderate | Moderate |
Drying Times | Slow. Can be increased with curing chamber | Fast | Slow. Can be increased with heating | Slow. Can be increased with heating | Slow. Can be increased with heating |
Coating Speeds | Slow | Very slow | Fast | Fast | Slow |
Parameters Affecting Coating | Withdrawal speed Solution properties | Rotation speed Rotation time Solution properties | Solution flow rate Substrate speed Gap height Coating width Outlet thickness Upstream pressure difference Attack angle Head design Solution properties | Gap height Substrate speed Solution properties | Wire diameter Solution properties |
Supported Reading
M. A. Aegerter & M. Mennig. Sol-Gel Technologies for Glass Producers and Users.
Slot Die Coating Head Design
Slot Die Coating Designs
To the best of our knowledge, the technical information provided here is accurate. However, Ossila assume no liability for the accuracy of this information. The values provided here are typical at the time of manufacture and may vary over time and from batch to batch.